Understanding how information is presented on a wiring harness 2D drawing is the key to accurate interpretation. While different companies may use varying formats, the core principles remain consistent. To help you master wire harness blueprint reading, here are the 7 most important aspects to focus on:
Introduction to LSR Overmolding Technology
In today’s competitive manufacturing landscape, choosing the right material and molding technique is critical to product performance, cost-efficiency, and market success. Among the cutting-edge technologies, liquid silicone rubber (LSR) overmolding with plastics stands out for its unique benefits and wide-ranging applications. This article provides an in-depth overview of LSR overmolding, detailing its properties, processes, benefits, applications, and future trends.
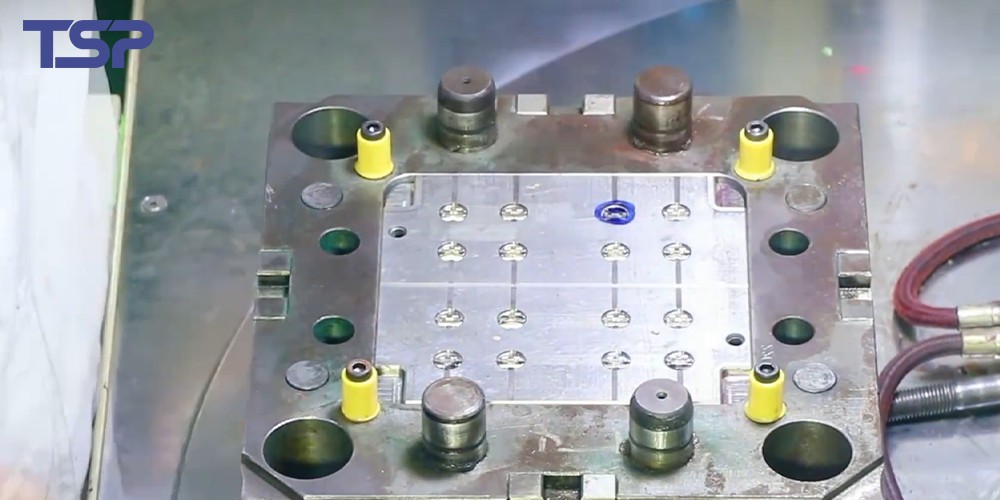
1. What is Liquid Silicone Rubber (LSR)?
Liquid silicone rubber (LSR) is a high-purity, two-component platinum-cured silicone material known for its excellent elasticity, thermal stability, and biocompatibility.
Key Properties of LSR:
High Temperature Resistance: LSR withstands temperatures above 250°C without losing its mechanical properties, making it ideal for extreme environments.
Biocompatibility: Suitable for medical and healthcare applications, LSR does not cause allergic reactions or adverse effects when in contact with human tissue.
Chemical Stability: Highly resistant to chemicals, LSR does not degrade easily over time or react with surrounding substances.
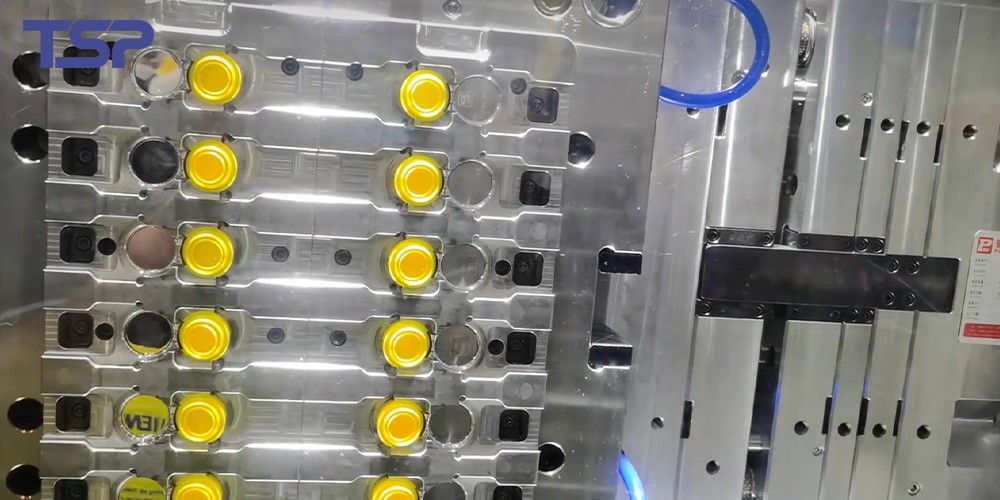
2. What is LSR Overmolding with Plastic?
LSR overmolding is an advanced injection molding process that combines LSR with thermoplastics like polypropylene (PP), polycarbonate (PC), or polyurethane (PU) in a single, integrated molding cycle. This results in a multi-material component with both hard and soft features.
LSR Overmolding Process Flow:
Mold Design: Precision-engineered molds are developed to ensure strong chemical and mechanical bonding between LSR and plastic.
Plastic Injection: The base structure is formed by injecting thermoplastic into the mold.
LSR Injection: LSR is then injected into predefined mold areas over or around the plastic.
Curing: The mold is heated to cure the LSR, creating a permanent bond with the plastic component.
Equipment Requirements:
A dual injection molding machine or combination of thermoplastic and LSR injection units.
Accurate temperature and pressure control systems.
Specialized molds with thermal isolation zones to manage different curing needs.
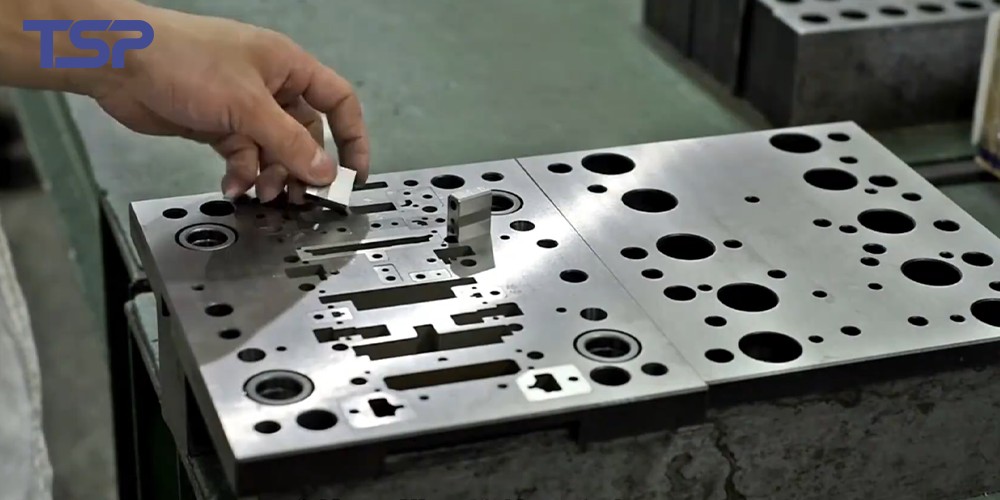
3. Advantages of LSR Overmolding
LSR overmolding offers multiple production and performance benefits, making it a preferred technology across industries.
Top Benefits:
✅ High Production Efficiency: Reduces labor and assembly time through single-step manufacturing.
✅ Enhanced Product Design Flexibility: Allows complex geometries and aesthetic surface finishes.
✅ Superior Mechanical Properties: Combines rigid support with soft, flexible comfort or sealing.
✅ Lower Material Waste: Optimized molding leads to minimal scrap and high material utilization.
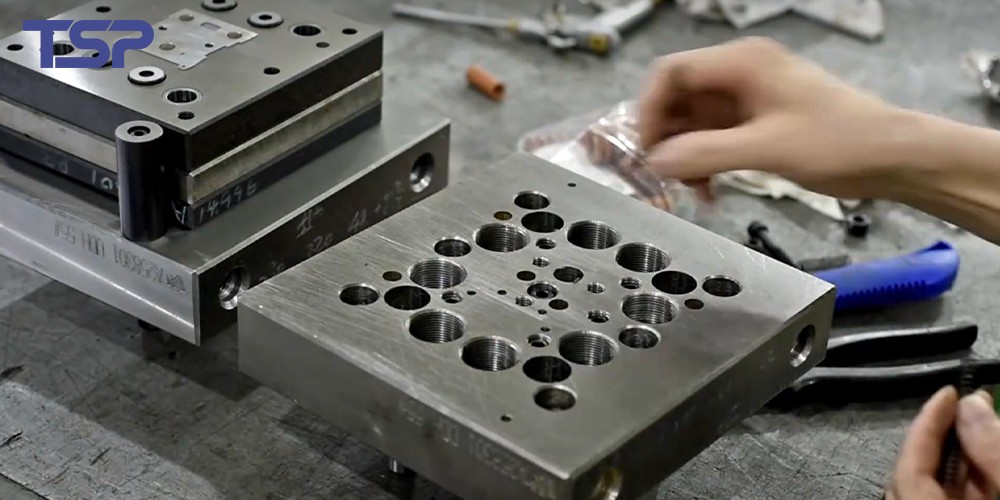
4. Applications of LSR Overmolding
LSR overmolding is widely adopted across industries that demand durable, high-performance, and safe products.
Key Application Areas:
Electronics: LSR improves waterproofing, impact resistance, and insulation in electronic devices.
Medical Devices: Due to its biocompatibility, LSR is ideal for wearable medical components, tubing, and connectors.
Consumer Products: LSR is used in baby products, kitchen utensils, and personal care tools for safety and comfort.
Automotive Industry: Common in soft-touch interior parts, gaskets, and vibration-damping components.
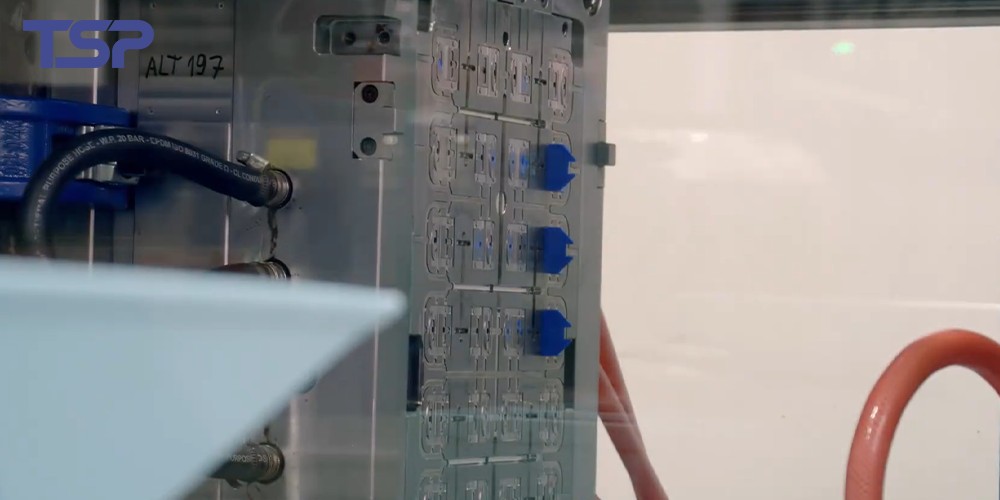
5. Future Trends in LSR Overmolding
As technology evolves, LSR overmolding continues to expand in capabilities and market reach.
Emerging Trends:
Smart Manufacturing: Integration of digital and automated technologies for real-time process monitoring and optimization.
Material Innovation: Development of new LSR and thermoplastic combinations for enhanced durability, color diversity, and functionality.
Sustainability: Adoption of eco-friendly materials and recyclable LSR grades to meet growing environmental standards.
Customization & Miniaturization: Growth in demand for customized and compact overmolded components in wearables, IoT devices, and personalized medical equipment.
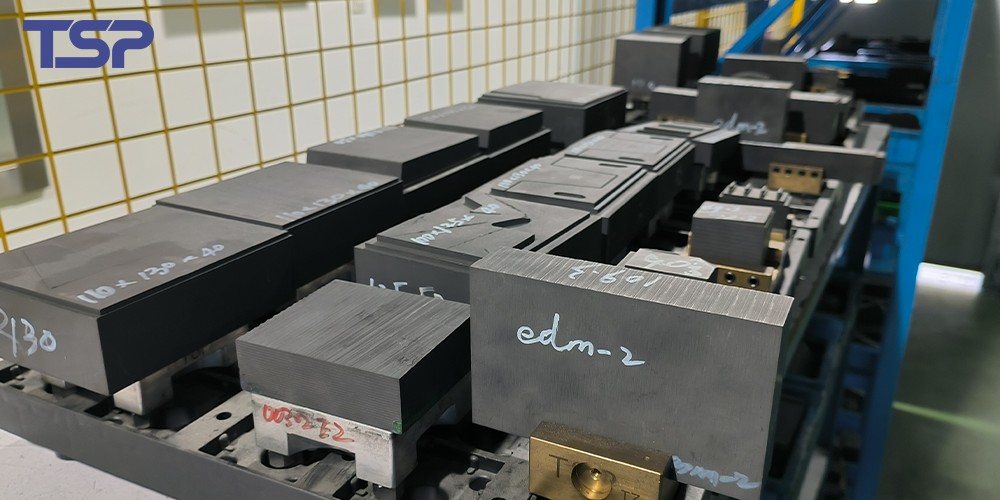
Conclusion
Liquid silicone rubber overmolding with plastic represents a powerful manufacturing solution that combines functionality, aesthetics, and efficiency. With increasing demand across industries such as automotive, healthcare, electronics, and consumer goods, this process is set to drive innovation and shape the future of multi-material product design.
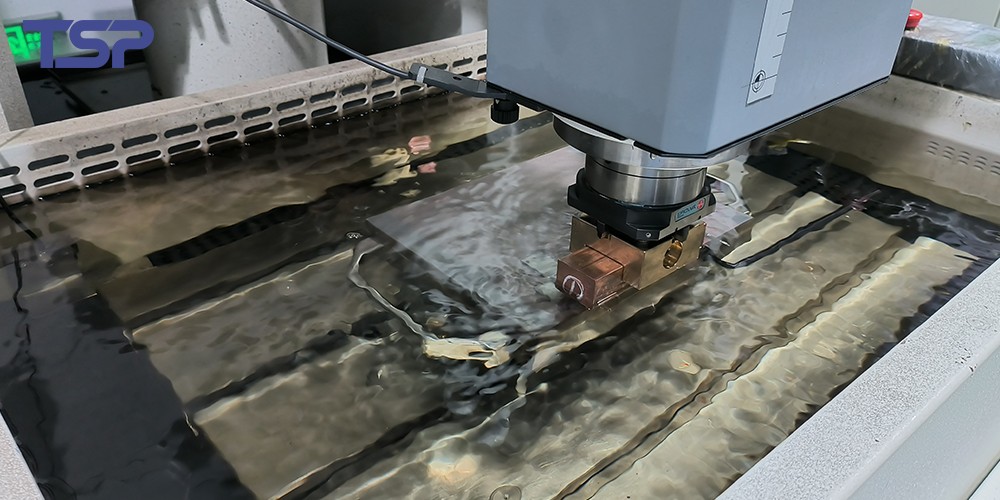
To read more: TSP Shanghai Achieves 1000KW Solar Power Milestone