Hot runner systems have become an essential component in the world of plastic injection molding over the past 70 years. They significantly enhance both production efficiency and product quality, providing solutions that address various challenges faced by manufacturers.
A hot runner system consists of a heated manifold and nozzles that maintain the molten state of thermoplastic material throughout the molding process. This continuous flow of plastic prevents solidification, unlike traditional cold runner systems, which require runners to cool and solidify before they can be removed. Hot runners offer a wide range of benefits, making them a popular choice in various industries.
What Is a Hot Runner System?
A hot runner system comprises a heated manifold and strategically placed nozzles in the injection mold. This system ensures that the plastic stays in a liquid state, allowing it to flow seamlessly through the runners to the mold cavities. The heated system is thermally isolated from the rest of the mold to keep the material at the desired temperature, allowing for precise flow control, minimizing waste, reducing cycle times, and improving the quality of the molded parts.
Hot runner systems are commonly used for both thermoplastics and crosslinking materials like elastomers and thermosets. Their ability to manage the flow of materials more efficiently has revolutionized the way plastic parts are produced.
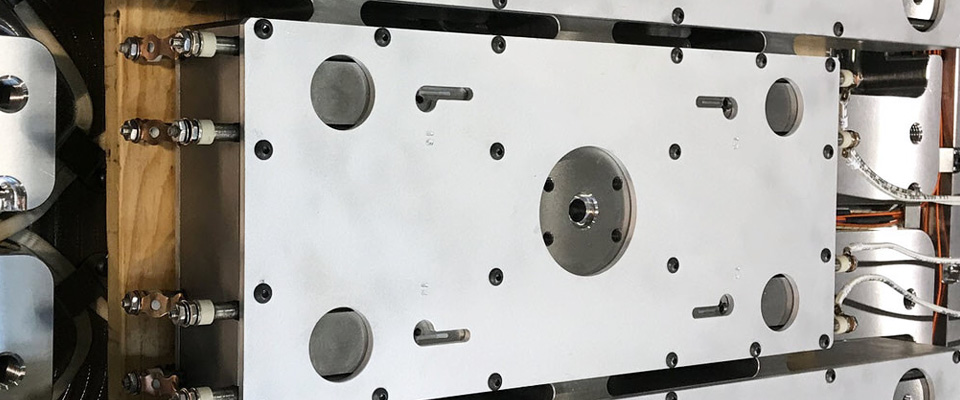
A Brief History of Hot Runner Systems
The development of hot runner systems began in the mid-20th century as industries sought to improve injection molding efficiency. In the 1960s and 1970s, early hot runner systems emerged, with companies like Mold-Masters and Husky Injection Molding Systems leading the way. These systems focused on improving temperature control and reliability. In the 1980s, companies such as Incoe Corporation made significant contributions with enhanced designs, improving both system functionality and precision.
Advantages of Hot Runner Systems
Material Efficiency
One of the most significant advantages of hot runner systems is the elimination of waste. Unlike cold runner systems, where plastic solidifies in the runners and must be discarded, hot runner systems keep the material molten. This reduces the need to regrind and reprocess waste, which is especially beneficial when using costly or specialized thermoplastics.
Faster Cycle Times
Hot runner systems eliminate the need to wait for runners to cool, thus reducing cycle times. As a result, production rates increase, and overall efficiency improves. Additionally, smaller machines can be used, as hot runners reduce the required shot volume and clamping force.
Improved Part Quality
The precise control of material flow reduces defects like uneven filling, flash, and sink marks. Hot runner systems also offer better control over gating positions, leading to smoother material flow and improved aesthetics. Advanced technologies like valve gate nozzles and cascade gating further enhance part consistency, reducing defects and enhancing part quality.
Optimized Material Flow
Hot runners allow for larger runner diameters and reduced pressure losses, making it easier for material to flow through the mold. This leads to smoother molding processes, with less stress on the injection unit and reduced clamping force demands.
Enhanced Dimensional Accuracy
With the ability to maintain uniform holding pressures, hot runner systems reduce shrinkage and warpage in molded parts. This results in improved dimensional accuracy, tighter tolerances, and stronger parts.
Disadvantages of Hot Runner Systems
Thermal Degradation
One of the main drawbacks of hot runner systems is the potential for thermal degradation of sensitive materials. If the plastic stays in the heated manifold for too long (high residence time), it can degrade, which may be problematic for materials with narrow processing windows. Careful temperature control is crucial to avoid such issues.
Complex Maintenance
Hot runner systems are more complex than traditional cold runner systems and require regular maintenance to ensure optimal performance. Issues like leaks, clogging, or malfunctioning heaters can disrupt production and incur additional costs.
High Initial and Operating Costs
Hot runner systems tend to have a higher initial investment than cold runner systems. Additionally, the need for precise temperature control and frequent maintenance can lead to higher operational costs over time.
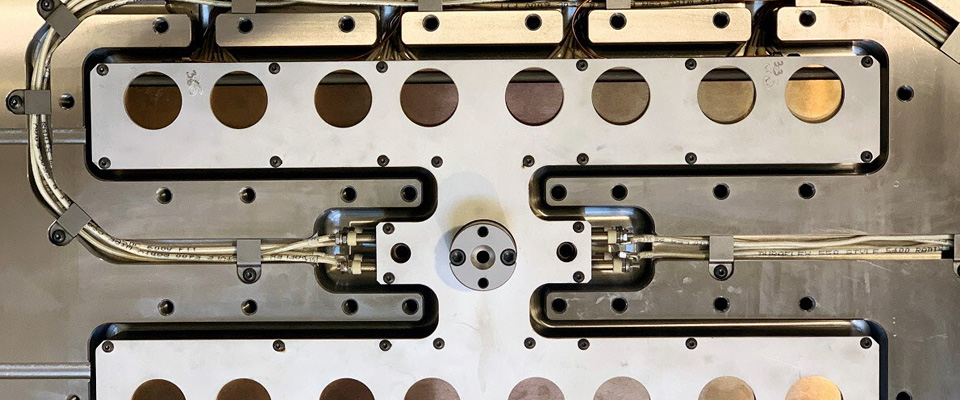
Conclusion
Hot runner systems offer significant advantages, such as material savings, faster production cycles, and improved part quality. However, they also come with challenges, including higher upfront costs and the need for meticulous temperature control and regular maintenance. For industries that require high-volume production of precision parts, the benefits of hot runner systems far outweigh the disadvantages, making them an indispensable tool in modern injection molding.