Plastics injection molding (IM) is a dominant plastic processing method, accounting for nearly 50% of all plastic production techniques. Compared to processes like blow molding or thermoforming, injection molding is favored for its ability to create complex parts with high repeatability and minimal waste.
In the fast-paced realm of manufacturing, injection molding has emerged as a transformative process. It facilitates the production of everything from everyday household items to intricate components for high-tech industries. According to recent market analysis, the global injection molding market was valued at approximately $270 billion in 2023, with projections to reach $357 billion by 2027.
What is Plastics Injection Molding?
Injection molding is an innovative manufacturing process that produces parts by injecting molten plastic into a mold. It is one of the most common methods for mass-producing plastic products, consisting of several key steps from pellets to finished parts:
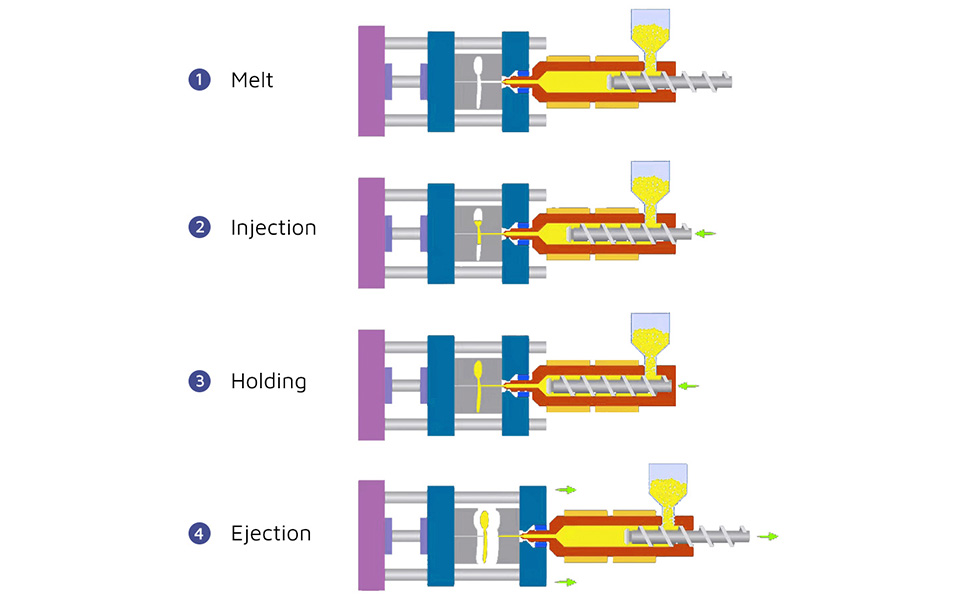
1. Feeding
Plastic pellets are poured into a hopper.
2. Melting
After that, the pellets are conveyed into a heated barrel-screw system, where they are melted by both heat and friction.
3. Filling
Consequently, the molten plastic is injected into the mold cavity through a nozzle.
4. Cooling
During the time the mold is closed and the filling is finished, the plastic cools and solidifies within the mold, forming the desired part shape.
5. Ejection
Finally, the mold opens, and ejector pins push the finished part out of the mold.
Key Components of Injection Molding
Machine
The main equipment that melts the plastic and injects it into the mold, comprising a hopper, barrel, screw, and clamping unit.
Mold
A custom-designed tool that shapes the molten plastic, consisting of two halves: the cavity (female) and the core (male).
Material
Common materials include thermoplastics, elastomers, liquid silicone rubber (LSR), and thermosetting resins, chosen based on application needs.
Part Design
The design must consider factors like uniform wall thickness, material flow, and cooling time to ensure high quality and feasibility.
Process Control
Managing critical variables such as injection pressure, temperature, and cooling time ensures the production of consistent, high-quality parts.
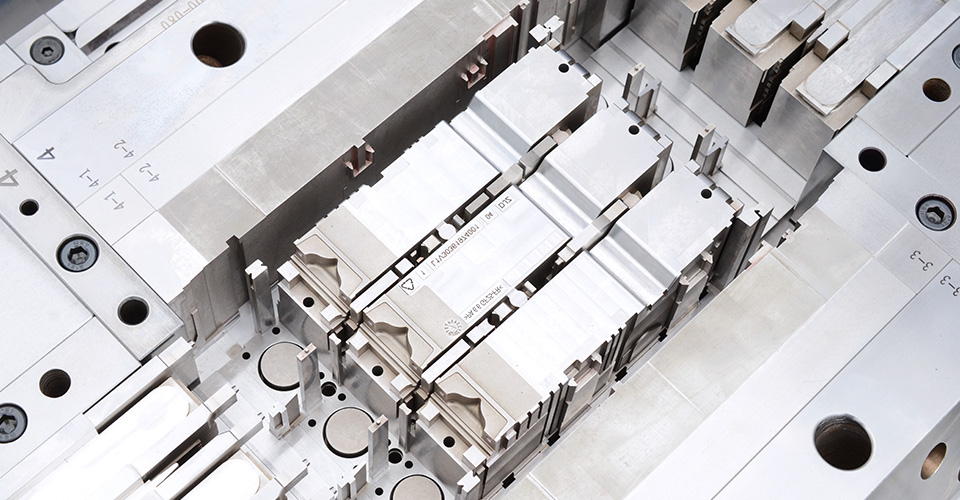
Advantages and Disadvantages
Understanding the benefits and limitations of injection molding is essential for evaluating its suitability for various applications.
Advantages | Disadvantages |
---|---|
High Efficiency and Production Speed | High initial tooling and machine costs |
Ability to Produce Complex Designs | Long lead times for mold design and manufacturing |
Material Versatility | Part design restrictions due to the need for uniform wall thickness |
Cost-Effective for Large Production Runs | Not economically viable for small production runs due to setup costs |
Minimal Waste Production | Potential for defects such as warping, sink marks, and surface defects |
Consistent Quality and Precision | Requires careful control of process parameters to maintain quality |
Applications
Injection molding’s versatility spans numerous industries, including:
• Automotive: Production of dashboards, bumpers, and other components.
• Medical: Creation of medical devices, syringes, and surgical instruments.
• Consumer Goods: Manufacturing everyday items like toys, kitchenware, and packaging.
• Electronics: Production of housings for electronic devices, connectors, and various small components.
• Industrial: Fabrication of parts used in machinery and industrial equipment.
Latest Trends
The injection molding industry is continuously evolving, with advancements enhancing processes and outcomes:
1. Sustainable Materials and Processes
Increasing emphasis on biodegradable and recycled plastics is aligning with global sustainability efforts.
2. 3D Printing for Prototyping
3D printing enables the creation of prototype molds and tooling inserts, significantly reducing development time and costs.
3. Automation and IoT Integration
Automation and IoT technologies improve monitoring and control of injection molding machines, enhancing efficiency and product quality.
4. Advanced Simulation Software
New tools facilitate better simulation and modeling of the injection molding process, optimizing mold design and improving efficiency.
5. Micro Injection Molding
This technique produces extremely small parts with high precision, particularly useful in medical and electronic applications.
6. Smart Manufacturing and Industry 4.0
The integration of AI and machine learning is transforming injection molding, providing insights for predictive maintenance and process optimization.
Conclusion
Injection molding remains a cornerstone of modern manufacturing, offering unmatched efficiency, versatility, and precision. Its capability to produce complex designs and accommodate various materials makes it essential across numerous industries. As technology continues to advance, the process will evolve, promising greater capabilities and applications in the future.
By grasping the intricacies of plastics injection molding and staying informed about the latest trends, manufacturers can harness this powerful method to innovate and enhance their production processes, driving success across automotive, medical, consumer goods, electronics, and industrial sectors.