Injection molds are essential in manufacturing, and their longevity is a crucial factor in cost-efficiency and productivity. This article discusses the key aspects influencing mold life, including material choice, operating conditions, design considerations, and maintenance practices. It also offers insights from industry best practices to help maximize the lifespan of injection molds.
Understanding Mold Lifespan
The lifespan of an injection mold refers to the number of production cycles it can withstand before deteriorating. The Association of Plastics Industry classifies molds into five categories based on their expected performance:
Class 101
Premium quality molds designed for over 1,000,000 cycles, suitable for demanding industrial applications. They are made from high-grade materials, making them the most expensive option.
Class 102
Designed for up to 1,000,000 cycles, these molds provide a balance between durability and cost, ideal for medium-to-high volume production.
Class 103
With a lifespan of up to 500,000 cycles, these molds are suitable for moderate production needs, often used in mid-range quality applications.
Class 104
Designed for up to 100,000 cycles, these lower-grade molds are less durable and require more frequent maintenance.
Class 105
The most economical choice, with an expected lifespan of around 500 cycles, these molds are intended for prototypes or low-volume production.
Factors Influencing Mold Life
Several variables can affect the longevity of injection molds:
Material Selection
The choice of material significantly impacts durability. Steel is the most robust option, enduring many cycles, but it comes at a higher cost. Aluminum, while cheaper and easier to machine, has a shorter lifespan and is more prone to wear. Steel molds are ideal for large-scale production, whereas aluminum molds are often used for prototyping and small-volume runs.
Operating Environment
A clean operating environment is vital for extending mold life. Exposure to dust, dirt, and corrosive substances can accelerate wear and lead to premature mold failure. Molds in controlled settings typically last longer.
Cycle Time and Production Speed
High-speed manufacturing and shorter production cycles can place additional stress on molds, particularly if cooling periods are insufficient. Allowing adequate cooling time between cycles helps mitigate thermal stress and extend mold life.
Preventive Maintenance
Regular maintenance is crucial for prolonging mold life. Practices such as cleaning, lubrication, and inspections help identify minor issues before they escalate into significant problems, ensuring molds perform optimally.
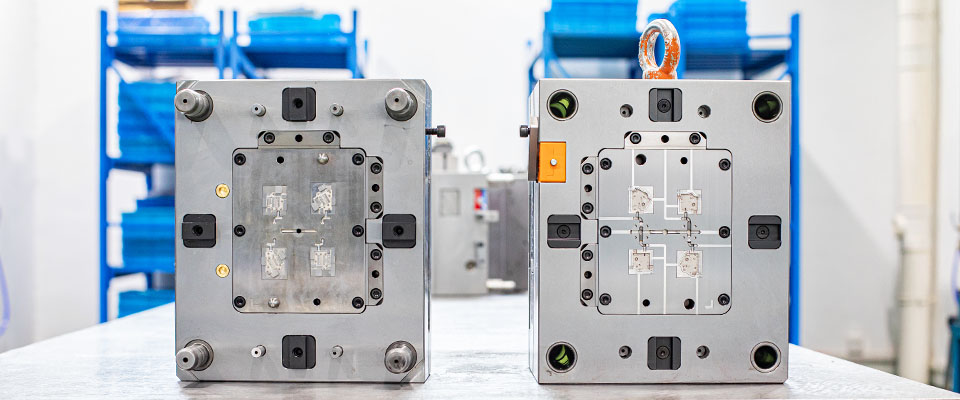
Best Practices for Extending Mold Life
Implementing best practices can significantly enhance the longevity of injection molds. Here are four strategies recommended by industry experts:
Optimal Mold Design
Design molds with features that promote even heat distribution to prevent hotspots. Incorporating cooling channels can help maintain consistent temperatures during the molding process.
Material Compatibility
Select appropriate materials for both the mold and the molded parts. For instance, molds handling abrasive materials should be made from durable steel, while less demanding applications may permit the use of aluminum.
Effective Venting and Cooling
Implement efficient venting systems to avoid air and gas pockets that can harm molds. Proper cooling is equally important to prevent thermal fatigue.
Surface Treatments
Applying surface treatments like Physical Vapor Deposition (PVD) coatings can reduce friction, facilitating easier part ejection and minimizing wear.
Maintenance Strategies
A robust maintenance program is essential for mold longevity:
Regular Inspections
Schedule frequent inspections to monitor wear and tear, ensuring molds operate at peak performance.
Lubrication
Keep molds adequately lubricated to reduce friction and wear on moving parts. Neglecting lubrication can lead to increased stress and shortened mold lifespan.
Prevent Overheating
Avoid overheating during production to prevent warping, cracking, and other integrity-compromising issues.
Thorough Cleaning
Regular cleaning is vital to remove contaminants that could cause long-term damage.
Common Mold Defects
Even with diligent care, defects can occur during the injection molding process, affecting product quality and mold life. Some common defects include:
• Flow Lines: These occur when molten plastic cools unevenly, potentially creating weak spots.
• Sink Marks: Rapid cooling can cause depressions in the part, complicating ejection.
• Burn Marks: Excessive heat can lead to localized burn damage to both the mold and the part.
• Delamination: Layers separating during production can result in damage during ejection.
• Flashing: Excess plastic escaping along the parting line can cause mold damage over time.
Conclusion
Maximizing the lifespan of injection molds is vital for manufacturers looking to enhance cost-efficiency and productivity. By understanding the factors that influence mold longevity—such as material choice, operating conditions, and maintenance practices—manufacturers can extend the useful life of their molds. Additionally, adopting best practices in mold design, maintenance, and surface treatment can lead to significant cost savings and improved product quality.