Electrical Discharge Machining (EDM) plays a critical role in precision mold manufacturing, especially for high-value components like micro connectors, IC encapsulation molds, and LED molds. Despite advancements in high-speed milling, EDM remains essential for achieving fine details and tight tolerances in complex parts.
In this article, we explore how precision EDM contributes to ultra-high accuracy in mold fabrication, the key factors affecting machining quality, and how to control these variables for optimal results.
1. Why EDM is Essential in Precision Mold Manufacturing
Modern mold manufacturing demands increasingly tighter tolerances. EDM allows precise material removal without mechanical force, making it ideal for delicate or intricate mold parts. The core objectives of precision EDM are:
Dimensional accuracy: Tolerances within ±2–3μm
Profile fidelity: Sharp corners with R values < 0.02 mm
Flatness: Surface deviation ≤ 2μm from edge to center
Surface quality: Ra < 0.4μm (VDI 12), often mirror finish
Edge definition: No micro-chipping or edge burns > 0.015 mm
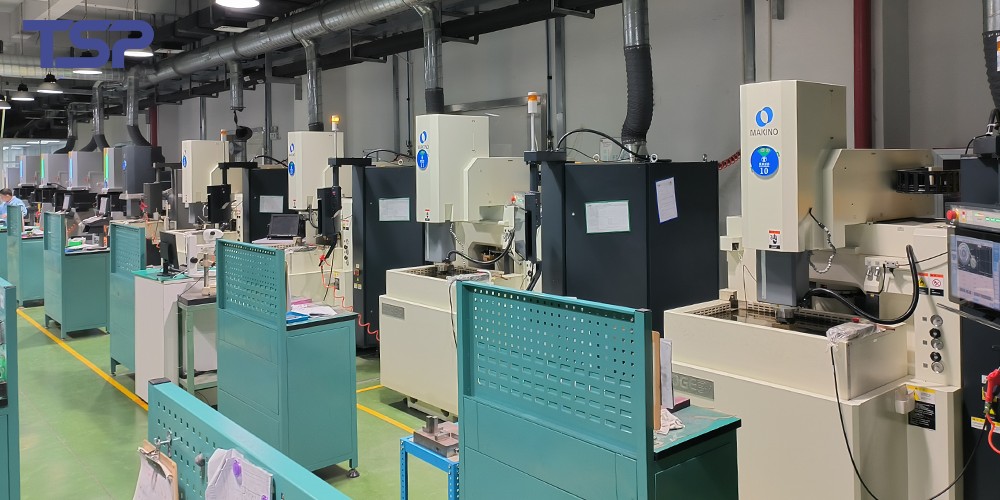
2. Choosing the Right EDM Machine for Precision Work
Precision depends largely on the EDM machine’s mechanical and control systems. Features to look for include:
Full-closed-loop control with high-precision optical scales
Stable micro-gap discharge control and pulse monitoring
Advanced servo systems to limit depth errors
Automatic electrode wear compensation
Multi-directional orbiting functions (like corner finishing and spherical motions)
High-speed jump machining to efficiently remove debris
High-end EDM machines also reduce reliance on operator skill by offering automation and AI-assisted processing.
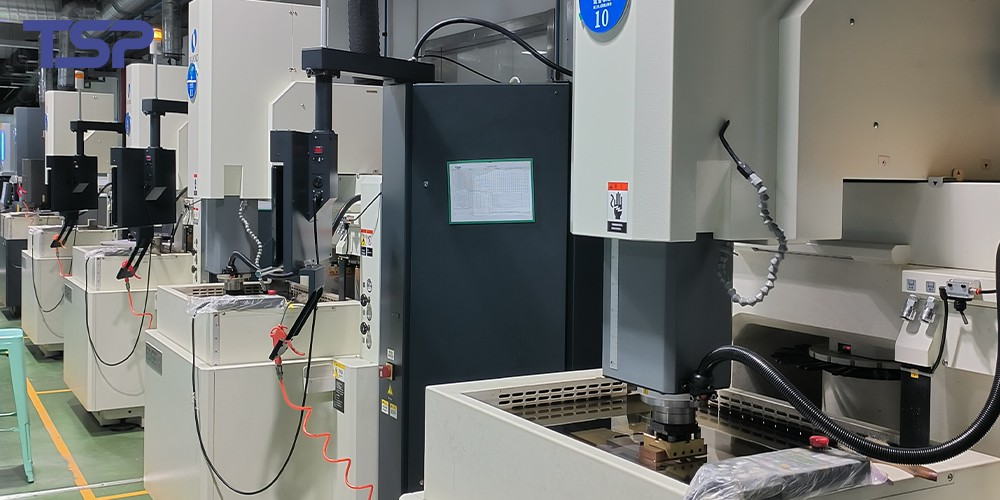
3. Multi-Electrode EDM Strategy
Precision EDM often employs multi-electrode machining:
Roughing electrode: Removes bulk material
Semi-finishing electrode: Prepares for fine finishing
Finishing electrode: Achieves final tolerances
Compensatory electrodes: Offsets electrode wear
Each electrode is scaled according to the discharge gap (typically 0.03–0.1 mm per side). Orbital motion during finishing further improves surface uniformity and reduces roughness, all while maintaining high profile accuracy.
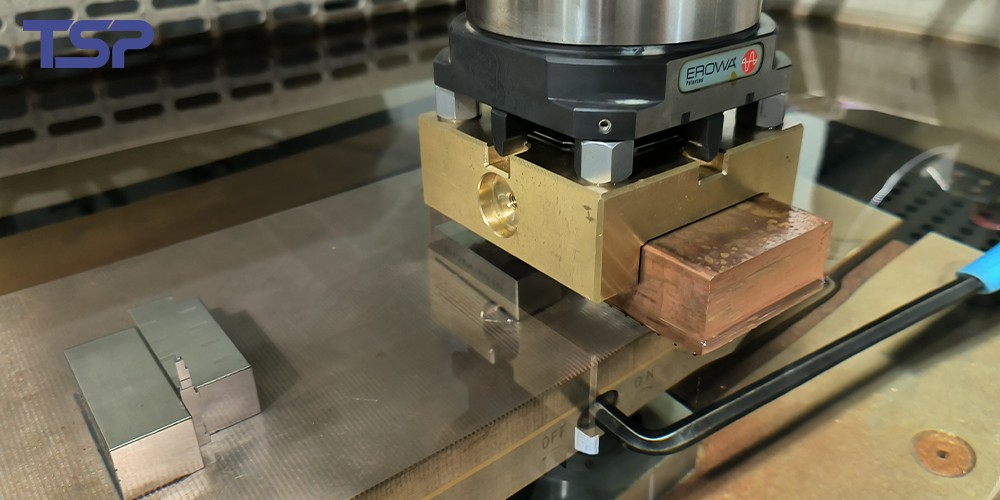
4. Ensuring Accurate Positioning in Precision EDM
Using quick-change clamping systems such as GF’s 3R enables electrode/workpiece swaps with ±2μm repeatability. Key techniques include:
Zero-point centering using reference spheres
Pre-machined locating surfaces for stable clamping
Clear electrode orientation marks and standardized depth references
High repeatability is crucial for post-measurement adjustments or multi-step finishing (re-machining after metrology).
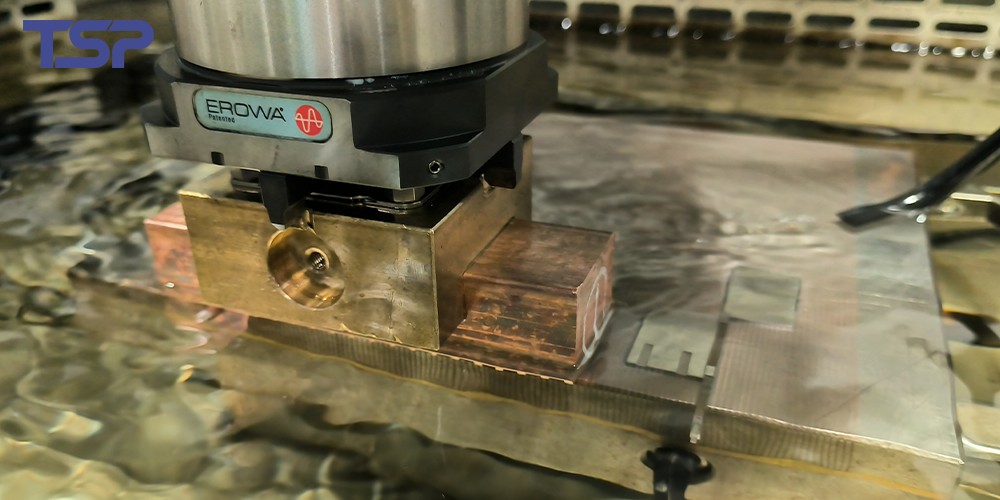
5. Precision Electrode Design and Manufacturing
High-quality EDM electrodes are essential. Requirements include:
Machined by high-speed CNC centers
Minimal post-processing or polishing
Made from high-performance materials, such as:
Copper (common and cost-effective)
Copper-tungsten alloy (for minimal wear in micro-EDM)
Each electrode should undergo detailed dimensional inspection before use. Poor electrode quality is a leading cause of part rejection in high-precision work.
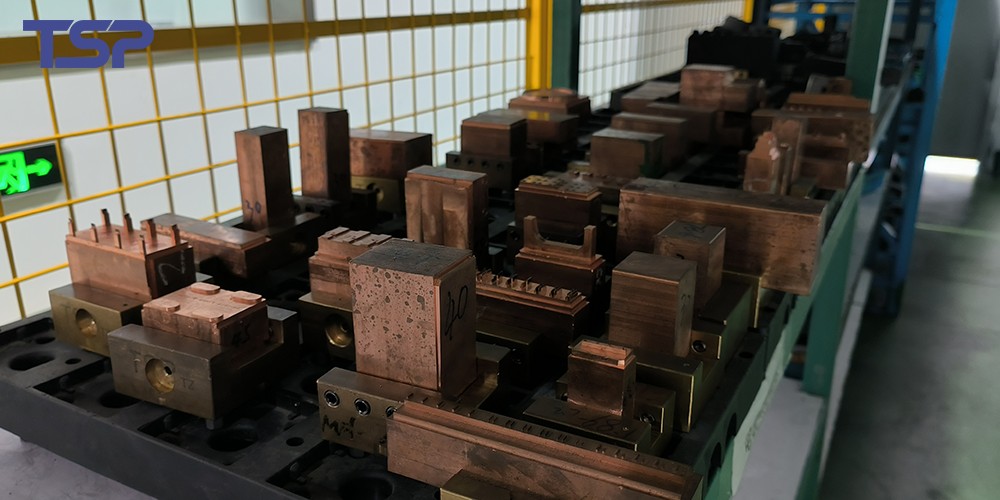
6. Intelligent EDM Parameter Control
Modern EDM systems use smart machining algorithms to monitor and adjust discharge parameters in real time. Recommendations:
Input accurate data for machining area, shape, taper, and surface finish
Avoid manually adjusting main pulse parameters unless necessary
Trust the EDM system to select the best conditions for each stage
This intelligent control maintains a stable spark gap and maximizes machining efficiency while ensuring surface integrity.
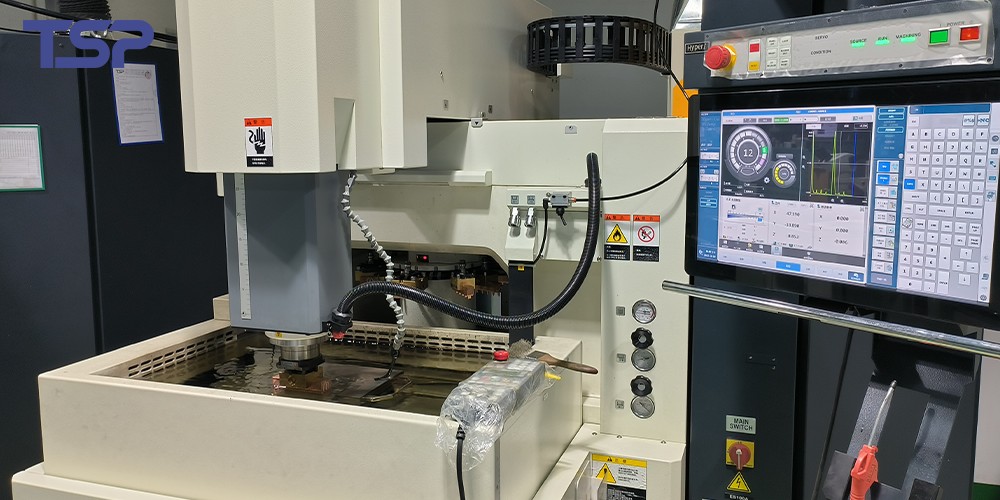
7. EDM Dielectric Fluid Management
EDM is performed in dielectric fluids that serve three functions:
Insulation during pulse discharge
Cooling of tool and workpiece
Debris removal from the spark gap
Precision EDM uses low-viscosity fluids and often relies on immersion machining with no flushing to prevent edge wear and uneven erosion. High-speed jump cycles and spindle acceleration aid in debris evacuation without disturbing the spark stability.
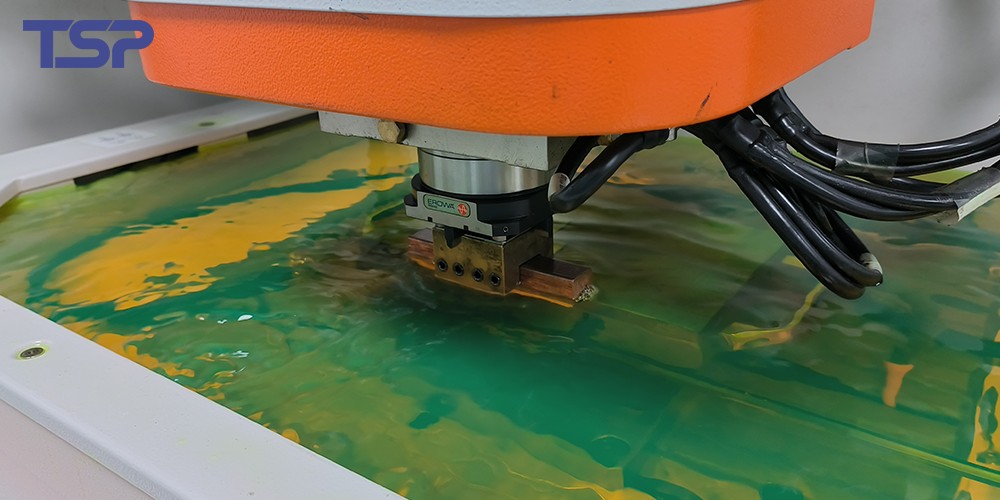
8. Post-Machining Adjustment: Finish Cuts (Re-cuts)
Due to inevitable machining deviations, final precision adjustments (known as finish or re-cuts) are required:
Start with a slightly undersized feature
Measure, analyze, and apply final cuts in clean conditions
Use automated re-positioning systems to ensure zero-point consistency
Finish cutting enhances final dimensional control and ensures critical tolerances are met.
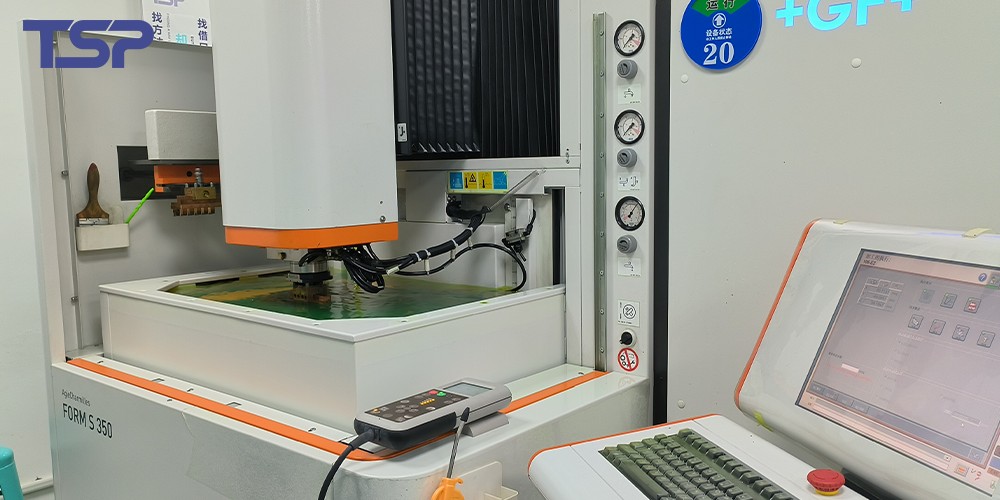
9. Standardizing the EDM Process for High-Precision Results
Precision mold EDM demands a standardized workflow:
Detailed electrode drawings, clear tolerance requirements, and material notes
3D references for complex features
Proper pre-treatment of workpieces: stress relief, de-magnetizing, rough machining
Polished locating surfaces to prevent contamination
All electrodes must be clearly marked with ID, type (rough/finish), shrinkage, tolerance, and Ra targets
Well-structured processes reduce human error and ensure consistent quality.
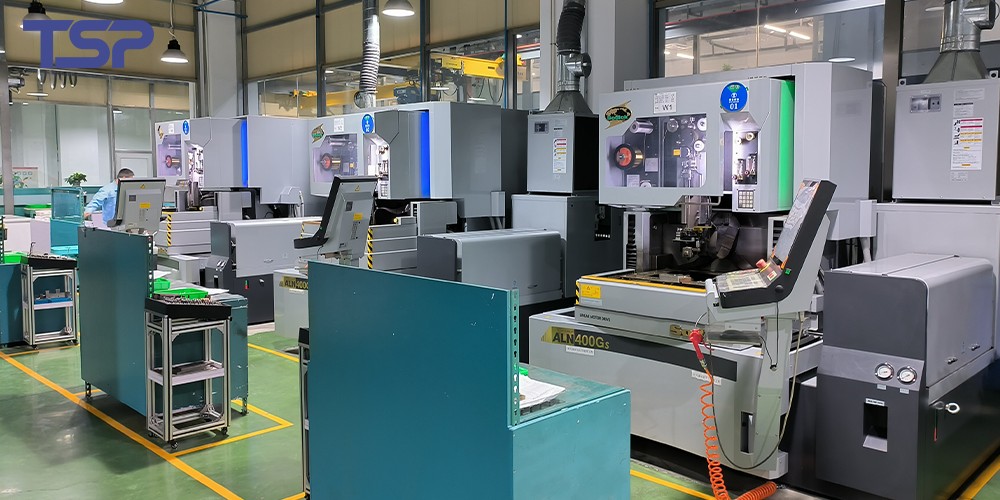
10. Environmental and Tooling Requirements
Environmental conditions significantly affect precision machining:
Temperature-controlled rooms (ideally 20±2°C)
Dedicated finishing zones to isolate vibration and dust
Precision tools: sine plates, gage blocks, micrometers, height gauges, dial indicators
Even minimal vibration or thermal expansion can impact measurements and machining results.
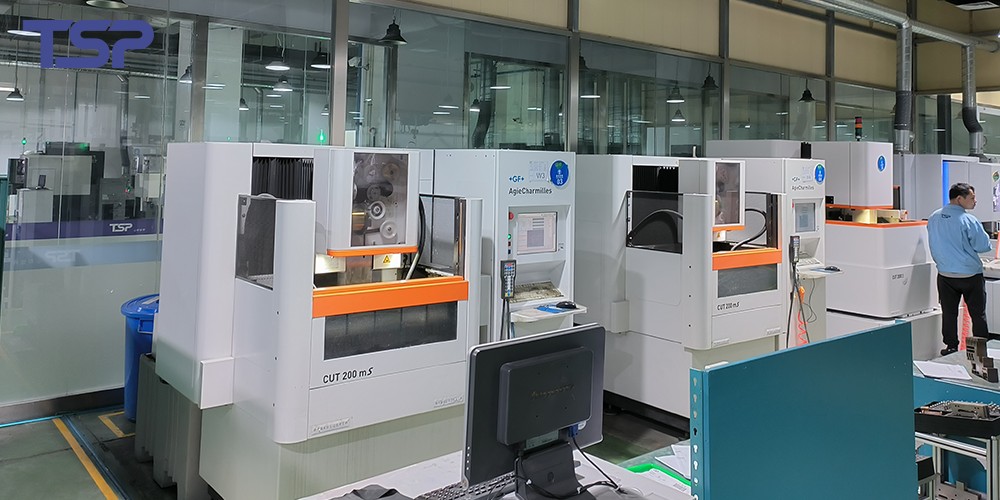
11. The Role of Skilled Operators in Precision EDM
Ultimately, precision EDM success hinges on well-trained, detail-oriented technicians who:
Understand each step of the EDM workflow
Can interpret 2D/3D drawings accurately
Control machining parameters based on part behavior
Maintain calm, focused work environments
EDM involves fine tolerances and low error margins, so operator competence is a decisive factor in achieving high-quality outcomes.
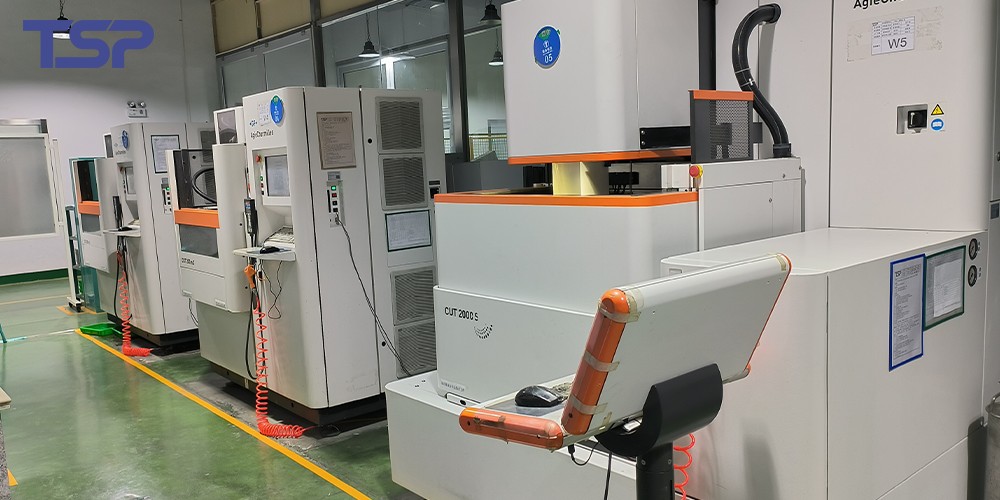
Conclusion: Achieving Ultra-Precision in EDM
Each step in precision EDM—from machine choice to fluid handling, from electrode design to re-machining—directly affects the final accuracy of mold components. By establishing a standardized, high-discipline process and relying on advanced machines and skilled personnel, manufacturers can meet the growing demand for high-value, micro-precision molds in electronics, automotive, and medical sectors.
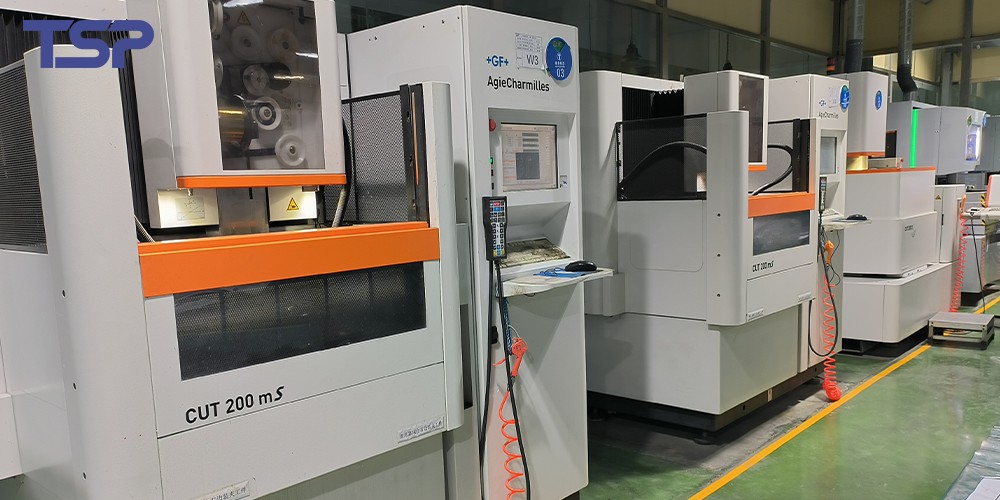
To read more: TSP Shanghai Achieves 1000KW Solar Power Milestone