With the rapid growth of the medical injection molding industry, manufacturers are facing an increasing number of challenges. From meeting personalized demands to ensuring strict quality control, each challenge impacts a company’s production efficiency and market competitiveness. Ensuring product quality and production efficiency has become a pressing issue for medical injection molding manufacturers. Custom injection molding, as a precise and efficient manufacturing technology, is gradually becoming the key to solving these problems. This article will explore the five major challenges faced by the medical injection molding industry and how custom injection molding can help companies effectively address these challenges.
Challenge 1: Meeting Personalized and Small-Batch Demands
Challenge Factors and Importance:
With the rise of personalized medicine, an increasing number of patients require specific medical injection molding products, such as custom implants, surgical instruments, and more. These products not only need to be precise but also tailored to individual differences. This presents a significant challenge for medical injection molding manufacturers, especially in small-batch production. The key issue lies in how to reduce costs while maintaining consistent product quality.
According to a report by McKinsey & Company, the demand for personalized medical injection molding products is expected to grow at a rate of 15%-20% globally in the coming years, particularly in fields like dentistry and orthopedic surgery, where the demand for personalized medical products is rapidly increasing.
Custom Injection Molding Solutions:
Custom injection molding can address small-batch and highly personalized demands by designing specialized molds and adjusting the production process. Injection molding not only supports high-precision manufacturing but can also reduce production costs through quick adjustments and multi-cavity designs, ensuring higher production efficiency even in customized production.
With flexible mold design and adaptable production scheduling, injection molding technology allows medical injection molding manufacturers to quickly respond to market needs while ensuring that each product meets strict quality standards.
TSP Case:
TSP provided custom injection molding services to a medical injection molding company, helping them successfully launch a series of personalized implants. Through TSP’s custom mold design, the client achieved small-batch production without sacrificing production efficiency, effectively reducing costs, and meeting the growing demand for personalized products.
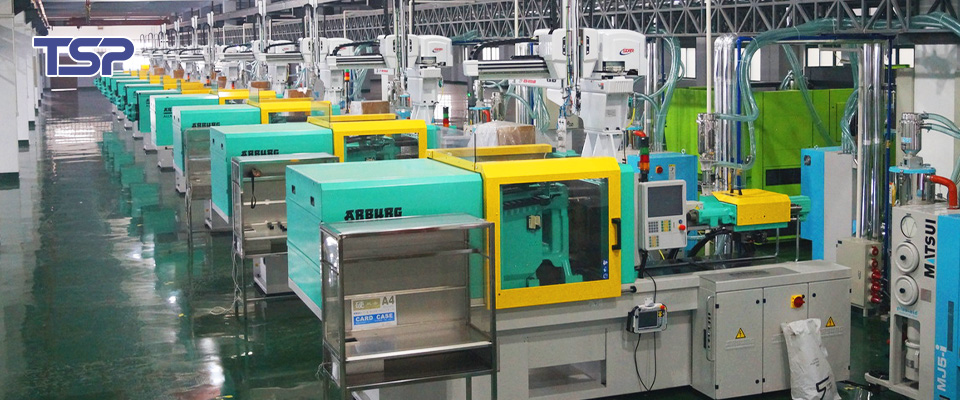
Medical injection molding production workshop
Challenge 2: Improving Product Precision and Quality Control
Challenge Factors and Importance:
The precision and quality control of medical injection molding products are directly linked to patient safety. Even the smallest deviation during production can lead to device failure, potentially endangering a patient’s life. However, traditional manufacturing processes often struggle to meet the strict precision requirements of medical injection molded products, especially when it comes to fine dimensions and shapes. As a result, ensuring the accuracy and consistency of every product has become a top priority for manufacturers.
According to the FDA, quality issues and deviations in precision are one of the leading causes of recalls for medical injection molding products. In recent years, the number of such recalls has steadily increased, putting significant pressure on manufacturers.
Custom Injection Molding Solutions:
Custom injection molding technology ensures precision and consistency in every product through high-precision molds and automated production lines. By leveraging the injection molding process, manufacturers can use real-time monitoring and adjustments during production to maintain high-quality standards and precise specifications.
The accurate design of injection molds and efficient production processes allow each medical injection molding product to meet exacting precision requirements, minimizing human intervention and reducing production errors.
TSP Case:
When TSP collaborated with a global leader in medical injection molding products, they successfully enhanced product precision using custom injection molding solutions. With TSP’s high-precision molds and automated production lines, the client’s product accuracy reached 0.01mm, significantly reducing defect rates and meeting multiple international quality certifications.
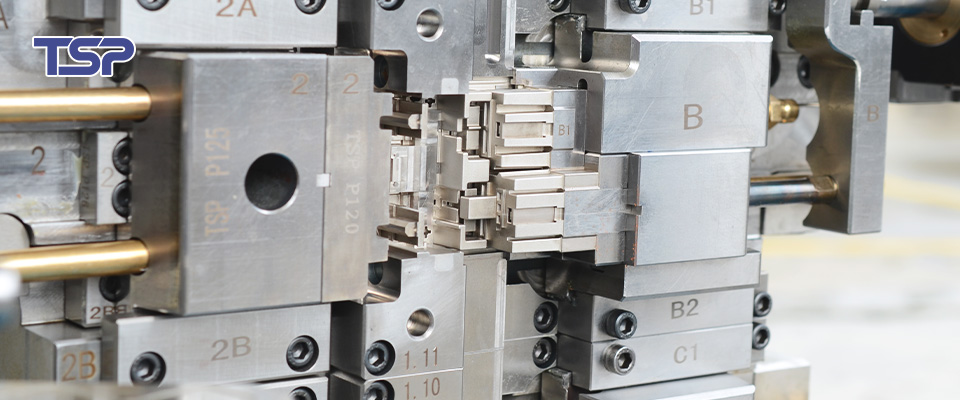
Customized injection molds
Challenge 3: Improving Production Efficiency and Reducing Lead Times
Challenge Factors and Importance:
As the demand for medical injection molded products continues to grow, manufacturers are under increasing pressure to shorten lead times and improve production efficiency. Traditional manufacturing methods often require longer production cycles and face challenges such as downtime and extended setup times during production.
According to a report by PwC, 30% of medical injection molding companies have stated that improving production efficiency and reducing lead times are key strategic goals for the next five years.
Custom Injection Molding Solutions:
Custom injection molding can significantly improve production efficiency through the use of high-efficiency mold designs and automated production technologies. One of the core advantages of injection molding is multi-cavity production and the ability to quickly switch molds, which helps minimize downtime, increase line productivity, and shorten the overall production cycle.
• Quick mold adjustments and replacements ensure the production line runs efficiently in a short amount of time.
• The introduction of automated production processes further reduces human error and enhances consistency and efficiency in production.
TSP Case:
TSP provided a custom injection molding solution for a medical injection molding company, reducing their production cycle by 30%. With TSP’s flexible mold design and automated production processes, the client not only boosted production efficiency but also was able to fulfill orders in a shorter timeframe.
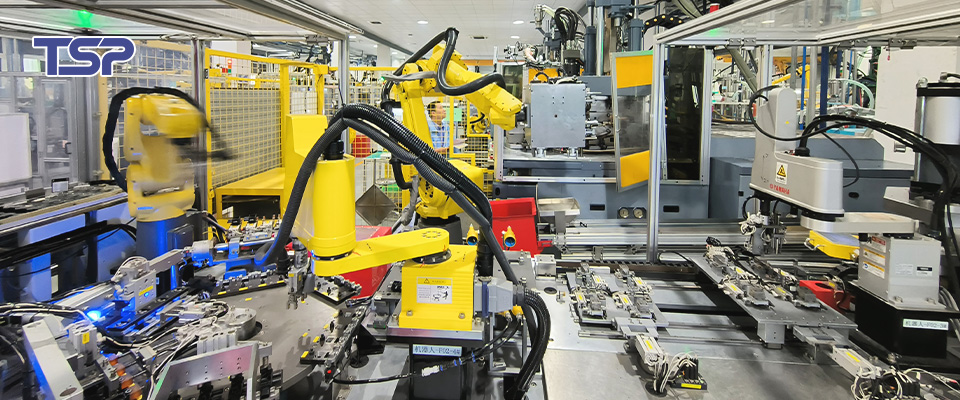
Production lines and automation equipment
Challenge 4: Controlling Costs and Maintaining Competitiveness
Challenge Factors and Importance:
In the highly competitive global market for medical injection molded products, effectively controlling production costs and improving the cost-performance ratio is another major challenge for manufacturers. With rising raw material prices and increasing labor costs, controlling expenses has become a crucial task for every medical injection molding manufacturer.
According to data from Grand View Research, the costs for medical injection molding manufacturers have risen by 3%-5% over the past five years, which has intensified the pressure of market competition.
Custom Injection Molding Solutions:
Custom injection molding can significantly reduce unnecessary material waste and lower scrap rates during production, thereby effectively controlling manufacturing costs through refined design and automated processes. In addition, custom injection molding helps companies maintain a cost advantage in a competitive market by optimizing production processes and enhancing efficiency.
• Precise material usage and efficient production methods effectively minimize waste during production.
• The cost reduction achieved through large-scale production allows clients to lower overall production costs while ensuring product quality.
TSP Case:
TSP helped a medical injection molding company reduce production costs by approximately 15% through custom injection molding technology. By optimizing production processes and selecting the right materials, the client not only controlled costs but also ensured the competitiveness of their products in the market, successfully expanding their market share.
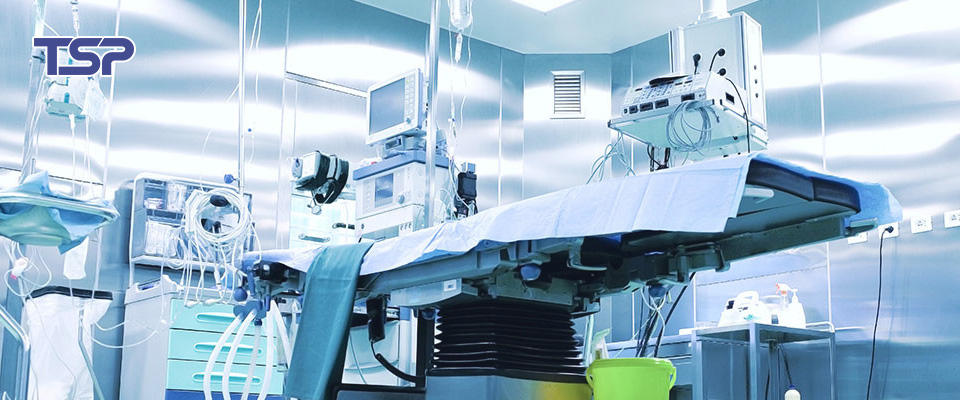
Scenarios of medical injection molding products in actual applications
Challenge 5: Ensuring Product Compliance with Industry Standards
Challenge Factors and Importance:
The production of medical injection molded products must comply with strict industry standards, such as FDA and CE certifications. These standards not only require products to meet specific quality requirements but also regulate every aspect of the production process. Any non-compliance can lead to challenges such as market access issues, recalls, and legal actions.
FDA and CE certifications are the most important compliance standards in the global medical injection molding industry. Products lacking compliance often face the risk of being rejected by the market.
Custom Injection Molding Solutions:
Custom injection molding processes ensure that each batch of products meets international and regional compliance standards through rigorous quality control and the selection of compliant materials. By strictly following quality management standards such as ISO 13485 during production, custom injection molding guarantees that products comply with all relevant industry certifications.
• Injection molding processes and material choices meet ISO 13485 and other international certification requirements, ensuring product quality and compliance.
• Automated production and quality control systems further ensure that every stage of the production process meets compliance standards.
TSP Case:
TSP provided a custom injection molding solution to an international medical injection molding company that met both FDA and CE certifications. The client highly praised TSP for its commitment to compliance and quality.
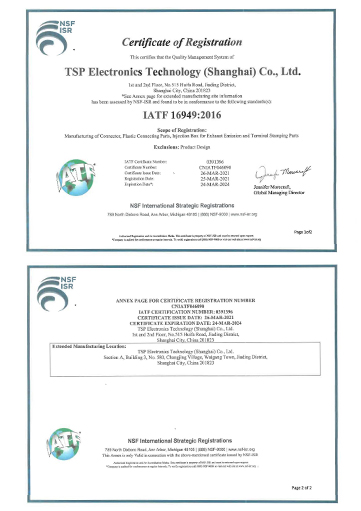
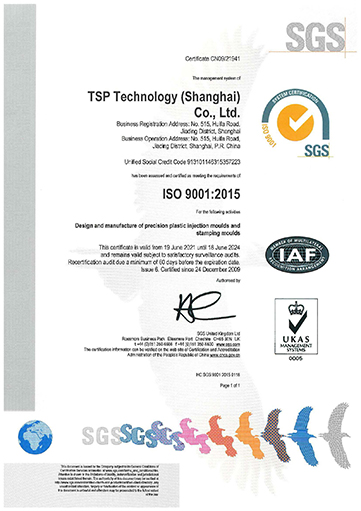



TSP Certifications
Conclusion and Call to Action
As the demands of the medical injection molded products industry become increasingly complex, custom injection molding technology is emerging as an effective tool to help manufacturers tackle these challenges. From personalized customization to precision manufacturing, custom injection molding offers highly competitive solutions for medical injection molding companies. If your company is facing similar challenges, TSP can help you achieve efficient, compliant, and cost-effective production solutions. Contact us to learn more and discover how TSP can provide tailor-made support for your project.