Medical injection molding products play a critical role in ensuring patient safety and effective medical treatment. However, product quality doesn’t just rely on design and material selection; it also hinges on every detail of the manufacturing process. According to the “Medical Device Quality Control” report, approximately 80% of medical product recalls are due to poor quality control during production. This underscores the importance of each step in the process. So, how can you ensure your medical injection molding products meet the highest standards? Here are seven key steps to help you improve the quality of your medical injection molding products.
1. Selecting the Right Materials: The Foundation of Quality
The quality of medical injection molding products begins with choosing the right materials. The medical industry has strict requirements for the materials used, especially those that come into prolonged contact with the human body. Medical products must meet ISO 10993 biocompatibility standards, undergoing biocompatibility testing to ensure they do not have adverse reactions when in contact with human tissue.
Commonly used materials such as polycarbonate (PC), polypropylene (PP), and polyethylene (PE) are known for their excellent biocompatibility and chemical resistance. When choosing these materials, it’s essential to ensure they meet medical-grade standards, as this directly impacts the product’s reliability and safety.
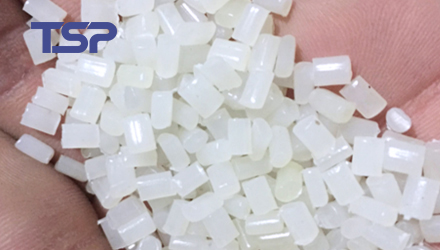
High-Quality Plastic Granules for Medical Products
Research from “Healthcare Materials Science” suggests that verified high-performance materials can significantly reduce defect rates in medical products and improve long-term reliability, highlighting the direct relationship between material quality and the overall safety and performance of the product.
2. Precise Mold Design and Manufacturing: Ensuring Accuracy and Consistency
Mold design and manufacturing precision are crucial for ensuring the quality of medical injection molding products, especially for devices that require high precision and complex structures. Molds must adhere to ISO 13485 quality management system standards to ensure that the design and manufacturing processes follow strict quality control procedures.
Medical injection molding products typically require mold tolerances of less than 0.05mm, as even slight deviations can result in non-compliant products. “Injection Molding Handbook” highlights that mold design precision, surface smoothness, and molding stability directly affect the functionality and safety of the final product, reinforcing the critical role that mold quality plays in the production process.
3. Optimizing Injection Molding Processes: Ensuring Consistency
Optimizing the injection molding process is another key factor in ensuring the quality of medical injection molding products. During production, the control of temperature, pressure, and injection speed directly affects product formation. Medical products require more precise process controls, with injection temperatures typically ranging from 250°C to 320°C to ensure product quality.
According to the “Medical Device Injection Molding” study, fluctuations in injection temperature can lead to 20% to 30% of products failing quality checks. This demonstrates how maintaining stability in the molding process—ensuring consistent temperature and injection speed—can effectively avoid defects such as bubbles or cracks.
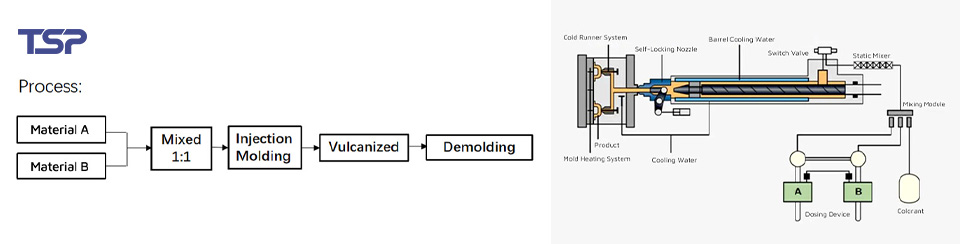
Injection Molding Processes
4. Rigorous Quality Control: Ensuring Compliance for Every Product
High-quality medical injection molding products depend on rigorous quality control. Each batch produced must undergo a series of inspections to ensure it meets the safety standards required in the medical industry. Medical products need to pass size inspections, strength tests, and chemical resistance tests to ensure compliance with ISO 9001 and ISO 13485 quality management system standards.
“Medical Device Regulation” notes that implementing a comprehensive quality management system can significantly reduce product failure rates, highlighting that strict quality control processes are essential to ensuring that each product meets the required specifications and reducing the number of non-compliant products.
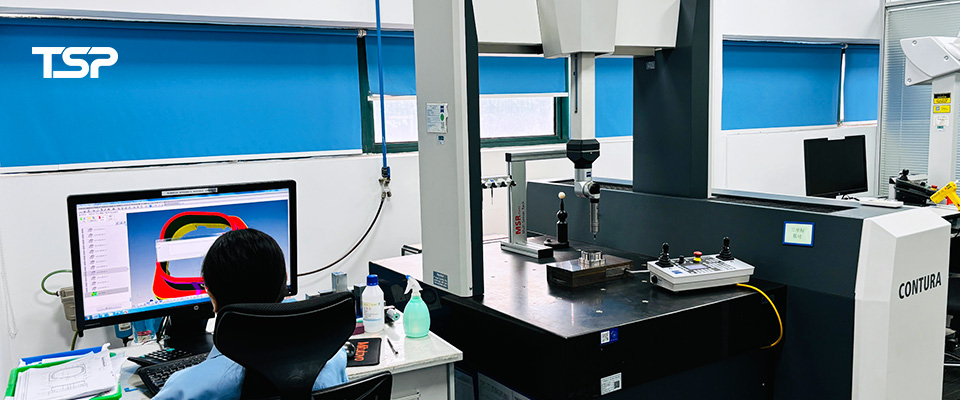
Quality Control Measurement Testing
5. Product Validation and Certification: Meeting International Standards
Medical injection molding products must meet a series of strict certification requirements to ensure they are legally marketable and safe for use globally. For example, the FDA in the U.S. has stringent certification requirements for medical devices, and depending on the product’s classification, it may need to undergo clinical trials and independent validation. In the European market, medical injection molding products must obtain CE certification, demonstrating compliance with safety and health requirements in the European Economic Area.
According to the “Global Regulatory Strategy for Medical Devices”, 70% of product market entry success is linked to whether it has passed FDA or CE certification. These certifications ensure that the product meets international safety standards and provide additional trust for customers.
6. Post-Processing and Packaging: Enhancing Product Quality and Protection
The post-processing of medical injection molding products is not just for aesthetics but also essential for ensuring product functionality and safety. For example, burr removal and surface finishing are necessary to eliminate defects from the injection molding process, ensuring products do not have sharp edges that could harm patients.
Additionally, medical devices require antimicrobial packaging to ensure that the products remain uncontaminated during transportation and storage. According to “Pharmaceutical Packaging Technology,” appropriate post-processing and packaging can reduce return rates by up to 10%, making these processes especially critical in the medical industry, where product quality is directly linked to patient safety.
7. Ongoing Product Tracking and Feedback: Ensuring Long-Term Quality
Quality management of medical injection molding products does not end at production; continuous product tracking and customer feedback are equally important. Once a product is on the market, manufacturers must establish effective lifecycle tracking to identify and address potential issues. Regular customer feedback helps manufacturers continuously improve product design and manufacturing processes.
The “MedTech Quality Control” report indicates that effective lifecycle quality management can reduce product failure rates to below 3%, emphasizing that ongoing product monitoring and feedback are vital for ensuring long-term product quality.
Conclusion
Ensuring the quality of medical injection molding products requires attention to detail at every step of the manufacturing process—from selecting the right materials and optimizing mold designs to implementing rigorous quality control and post-processing techniques. By following these seven critical steps, you can ensure that your medical devices not only meet industry standards but also offer the highest level of safety, functionality, and reliability.
However, quality control doesn’t stop once the product leaves the factory. Ongoing tracking, feedback, and certification are crucial to maintaining the product’s integrity throughout its lifecycle. Partnering with TSP can help you navigate these complex processes with confidence, ensuring that your medical injection molding products are of the highest quality, compliant with international regulations, and trusted by healthcare professionals worldwide.
Ready to take the next step in improving your product quality? Reach out to us today to learn how our advanced injection molding solutions can meet your specific needs and help you deliver top-quality medical products to market faster and with greater reliability.
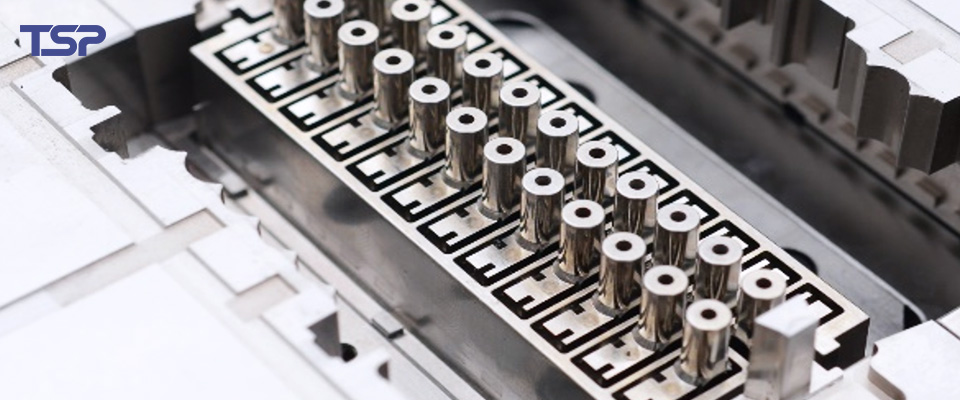
Precision Mold Processing