In electric vehicles (EVs) and hybrid systems, high-voltage (HV) wires are critical for transferring power between the battery, inverter, motor, and charging system. Choosing the right type of HV cable not only affects vehicle performance, but also determines long-term safety, stability, and efficiency.
This guide explains everything you need to know—from material selection to wire size and insulation type—in plain language, whether you’re a technician, buyer, or product manager.
🚗 Why High Voltage Wires Matter in EVs
Unlike traditional vehicles that use low-voltage (12V or 24V) systems, electric vehicles use much higher voltages, typically up to 800V or even 1000V.
These high voltages enable:
Faster charging
More efficient power transmission
Smaller cable sizes for same performance
But with higher voltage comes more technical requirements and safety concerns, which is why proper wire selection is essential.

🧱 Key Characteristics of High Voltage Automotive Wires
🟠 Color Identification
Orange is the standard color for high-voltage wires.
Often has a black or blue stripe to differentiate different signal or power lines.
Makes it easier to identify during installation or maintenance.
⚡ Voltage Rating
Most HV wires for EVs are rated for 600V–1000V DC.
Wires should pass high-voltage endurance tests like:
1000V for 30 minutes without breakdown
Instant surge test up to 5000V
🌡️ Temperature Resistance
Must withstand extreme temperature environments:
Continuous: -40°C to +150°C
Short bursts: up to 200°C
This protects the wire during fast charging, regenerative braking, or motor overheating.
🔰 Shielding (Electromagnetic Protection)
Motors, inverters, and battery systems generate EMI (electromagnetic interference).
Shielded HV cables protect other components (e.g., signal wires, ECUs) from interference.
Common shielding: tinned copper braid or aluminum foil, with high shielding effectiveness (≥85%).

🧪 Copper vs. Aluminum: Which Conductor to Use?
Material | Best For | Advantages | Disadvantages |
---|---|---|---|
Copper | Most EV wiring | High conductivity, durable, easy to crimp/weld | Heavy, more expensive |
Aluminum | Large cross-section cables (≥35mm²) | Lightweight, cost-saving | Lower strength, needs larger size |
🔍 Example:
To match the conductivity of 25mm² copper, you need around 42mm² aluminum.
👉 Aluminum cables are often used in battery-to-inverter connections or long-distance power delivery.

📏 How to Choose the Right Wire Size (Cross-Section)
Choosing the wrong wire size can result in:
Voltage drop (loss of power)
Overheating
Damage to insulation or connector
Worst case: fire or system failure
🔢 Key Considerations:
Operating Current
Match wire cross-section to your average load current
Use current–temperature derating curves provided by the cable manufacturer
Peak Load or Surge Current
During startup, acceleration, or fast charging, current can spike.
Wire must handle these brief surges without insulation damage
Ambient Temperature
Higher temperature = higher resistance
If routing through battery packs, engine rooms, or motor areas, choose a wire with extra heat tolerance
Fusing Coordination
Fuse rating should be lower than the point at which the wire emits smoke or burns
Always test wire + fuse combinations to ensure safe protection behavior
Connector Compatibility
Make sure the wire diameter fits into HV connector crimp barrels
Some systems use open-barrel or closed-barrel terminals

🧵 Types of High Voltage Wire Insulation Materials
Type | Features | Use Cases | Pros | Cons |
---|---|---|---|---|
Silicone Rubber (SI) | Very soft, handles up to 180–200°C | Battery packs, internal wiring, BMS | Flexible, high temp | Tears easily, costly |
Cross-linked Polyolefin (XLPO) | Tough and durable | Main power cables, underbody wiring | Good oil/abrasion resistance | Less flexible in cold |
TPE/TPU | Thermoplastic, high strength | Robot arms, EV charging | Good balance of cost/flexibility | Lower temp than XLPO |
Shielded Types | With copper braid or foil | Inverter, fast charger, motor wiring | Blocks EMI, stable signal | Higher cost, less flexible |
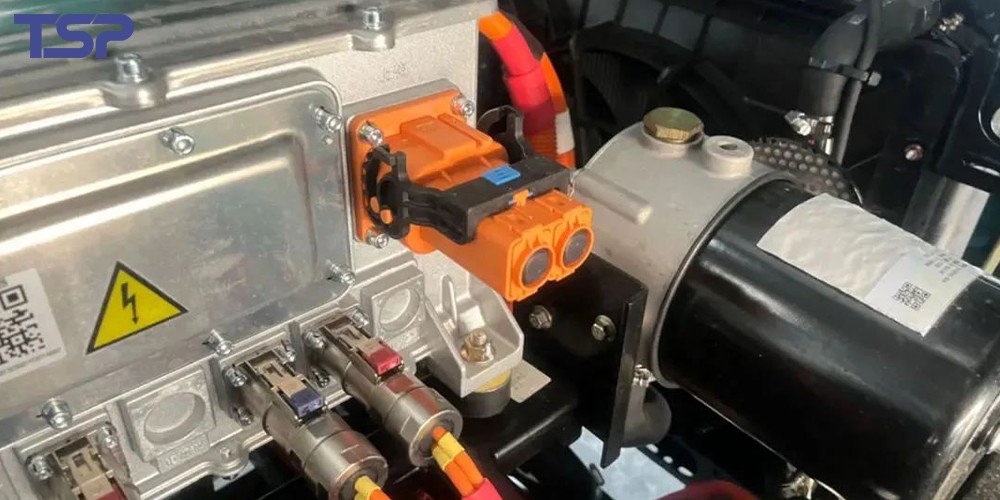
⚙️Common Applications for High Voltage Cables
Application | Typical Cable Specs |
---|---|
Battery to Inverter | 50–70 mm², shielded XLPO, up to 1000V |
Motor Drive Wiring | 25–50 mm², shielded, temp ≥150°C |
On-Board Charger (OBC) | 10–16 mm², single or double shielding |
High-Power Charging (Fast DC) | 70–95 mm², double shielded, highly heat-resistant |
Battery Module Jumpers | 6–16 mm², flexible silicone wire, short length |
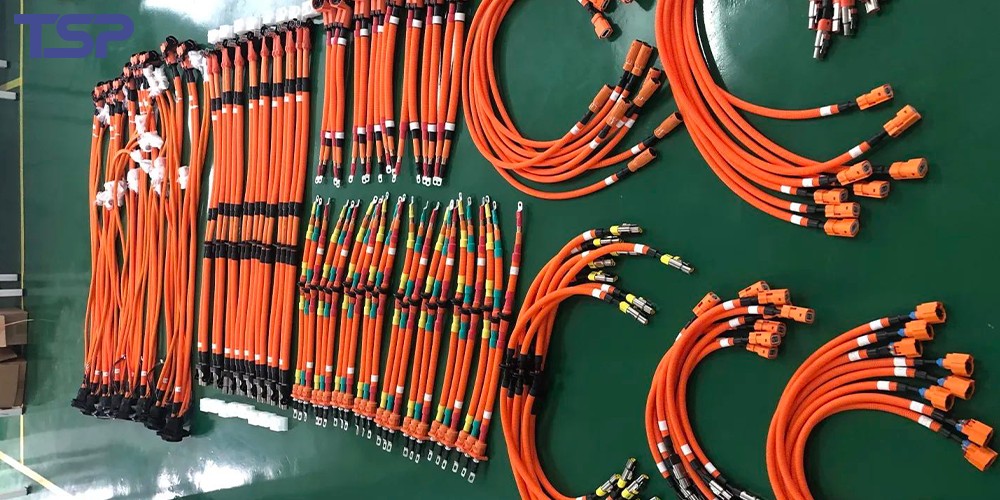
❓ Common Questions from Buyers
Q1: Can I use aluminum cables in place of copper?
✅ Yes, but the size must be increased, and terminals must support aluminum crimping.
Q2: What’s the most common size used?
🔌 Depends on the system, but 16 mm², 25 mm², and 35 mm² are popular for main power distribution.
Q3: Do I always need shielding?
💡 Not always. Shielding is needed near high-speed inverters, motors, and where EMI is a concern.
Q4: Can I use standard industrial cables for EVs?
⚠️ Not recommended. Automotive HV cables must meet standards like ISO 6722, LV 216, and ISO 19642.
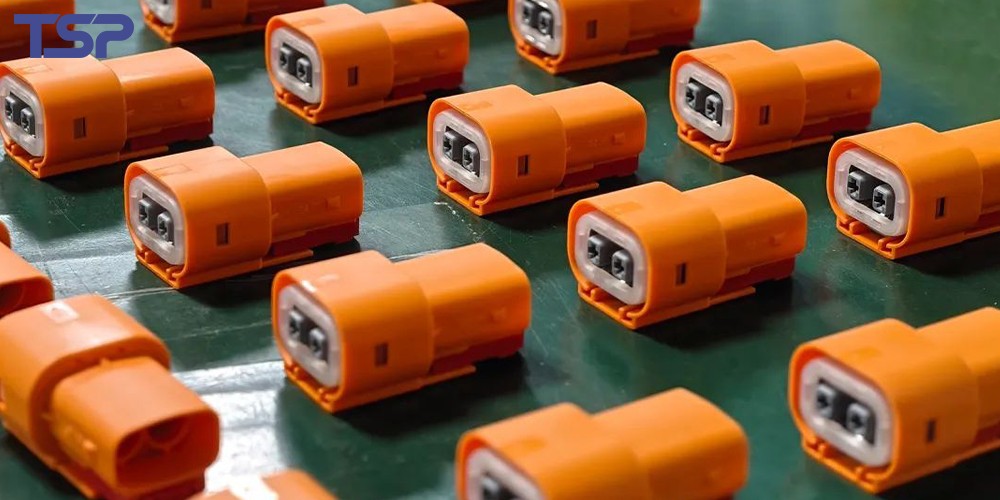
🧠 Final Checklist Before You Choose:
✅ Confirm working voltage and peak current
✅ Select suitable conductor (copper or aluminum)
✅ Choose proper insulation type based on usage
✅ Ensure compatibility with connectors
✅ Verify standards compliance (ISO, LV, RoHS, etc.)
✅ Test with fuse + harness for real-world validation
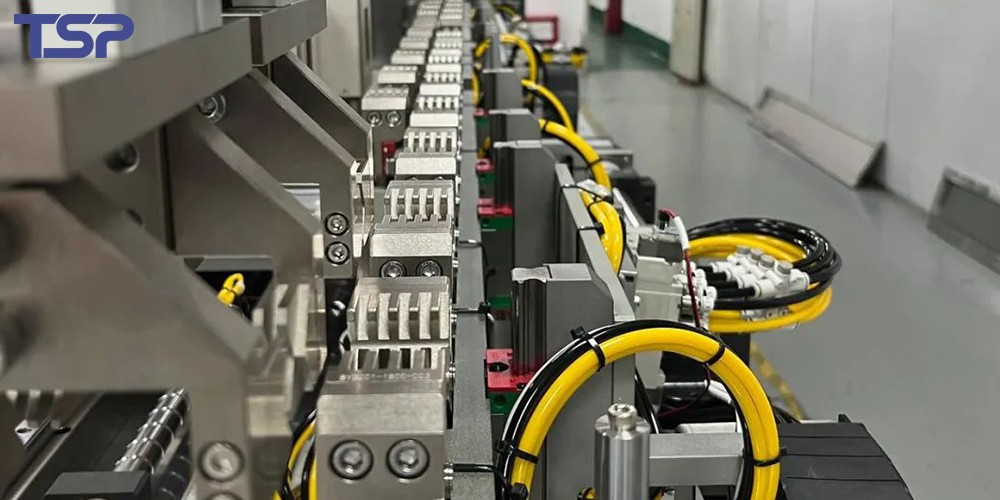
To read more: TSP Shanghai Achieves 1000KW Solar Power Milestone